

In addition, the average Yplus of the straight pipe, impeller, guide vanes and the elbow pipe were 27.9, 23.4, 11.2 and 33.3, respectively. The number of grid nodes of the straight pipe, impeller, guide vanes and the elbow pipe were 909,706, 1,746,876, 1,478,235 and 950,172, respectively. Therefore, the total number of grid nodes was finally determined as 5.41 million. When the number of grid nodes exceeds 5.41 million, the growth rate of pump efficiency is less than 0.02% and 0.2% under forward and reverse conditions, respectively. Figure 6 shows the grid independence analysis of the axial-flow pump. The grids of the straight pipe and elbow pipe were generated by CFD ICEM.
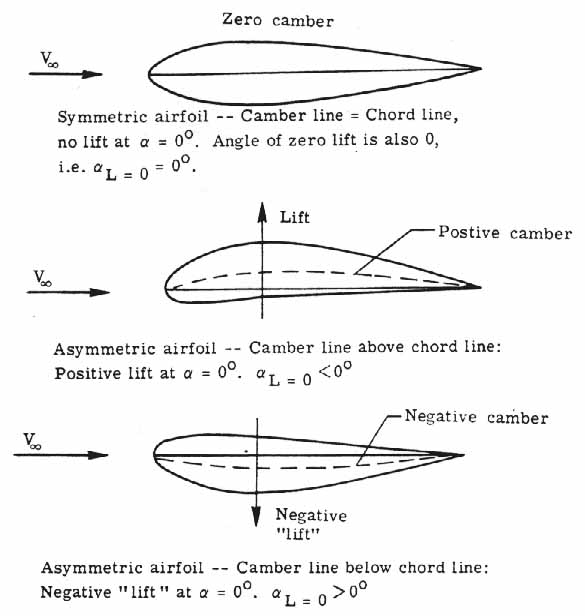
The impeller and guide vanes were generated by TurboGrid. The computational domain was entirely a hexahedral grid, and the grid at all wall surfaces was refined, as shown in Figure 5. However, there are few studies on the influence of airfoil camber on the pressure fluctuation characteristics in bidirectional axial-flow pumps, which makes designing a blade to control pressure pulsation difficult.

Ma compared the flow structure and pressure fluctuation in the bidirectional axial-flow pump and obtained the conclusions that the pressure fluctuation amplitude is higher under the reverse condition, due to the distorted impeller inflow induced by the inlet guide vane. He found that the amplitude of pressure pulsation increased caused by clearance flow.
#Airfoil camber full
Shi analyzed the effect of the backflow clearance on the pressure pulsation in the full tubular pump. The results showed that the timing effect can play a significant role in pressure fluctuation at the inlet and outlet of the impeller. In the axial-flow pump, Yang used time–frequency domain analysis to study the pressure pulsation characteristics at the impeller inlet, impeller outlet and guide vane outlet. Ji and Tan, respectively, analyzed the influence of blade tip clearance radius and blade rotation angle on the frequency domain of the pressure signal. The results showed that the hydraulic imbalance caused by the vortex and misalignment could cause the ellipse axis orbit of shaft frequency and two times the shaft frequency. In the mixed-flow pump, Li used a pressure sensor to measure the pressure fluctuation and impeller axis orbit. Zhang designed three schemes of splitter blades and suggested that deflecting the splitter blade to the suction surface of the main blade can reduce the pressure fluctuation. They found that the structure of an ellipse on the pressure side, an ellipse on both sides and bionic sinusoidal tubercle can effectively decrease the wake vortex intensity and pressure pulsation. Gao and Lin studied the effect of the trailing edge profile on pressure fluctuation. He believed that the appropriate blade-trailing cutting angle should be determined to effectively suppress the shedding vortex at the impeller outlet and reduce the pressure fluctuation. In the centrifugal pump, Cui found that the interference effect between the wake vortex and volute is the main source of severe pressure fluctuation, based on the detached eddy simulation method. The main frequency of the pressure signal near the impeller–straight pipe interface and impeller–guide vanes interface was the BPF, and the main frequency amplitude decreased with a decrease in airfoil camber angle.Īt present, the combination of numerical simulations and experimental measurements is used by many scholars to study the pressure fluctuation characteristics in different kinds of pumps. Under the reverse condition, the high PFI area near the inlet and the leading edge of the impeller declined with the decrease in airfoil camber angle. The main frequency of the pressure signal near the impeller–guide vanes interface was the blade-passing frequency (BPF), and the main frequency amplitude increased with a decrease in airfoil camber angle. Under the forward condition, the area of high PFI near the outlet and leading edge of the impeller increased with a decrease in airfoil camber angle, and that near the leading edge of the guide vanes shifted to the middle section with a decrease in airfoil camber angle. The results were validated by the external characteristic test. Fast Fourier transform was applied to analyze the frequency-domain characteristics of the pressure signal near the impeller–straight pipe interface and impeller–guide vanes interface.
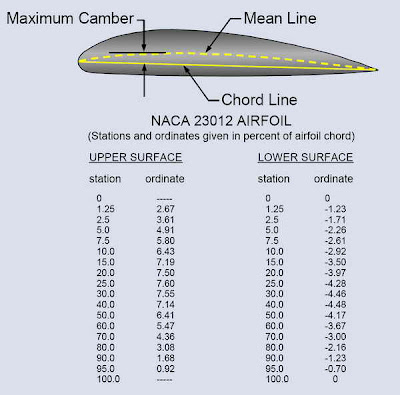
The pressure standard deviation was used to define the local pressure fluctuation intensity (PFI) inside the impeller and guide vane. The airfoil camber was quantitatively controlled by airfoil camber angle. To obtain the influence of airfoil camber on the internal pressure fluctuation of a bidirectional axial-flow pump, the unsteady Reynolds time-averaged Navier–Stokes (URANS) equation was solved to predict the internal flow structure under three airfoil camber cases.
